Better Buildings
ICF Technologies for Commercial and Residential Construction
What Makes a Better Building?
Stronger
Concrete structures are designed to last for centuries. Unlike other materials that will deteriorate, concrete gets stronger over time.
Insulated concrete forms are used to build reinforced concrete walls, resulting in a structure that is strong, durable and can stand up to mother nature.
While wood buildings can burn, rot, or be blown away by tornadoes and hurricanes, concrete buildings will withstand it all.
Quieter
Ask any developer about his number one complaint from tenants, and noise often tops the list.
Insulated concrete forms reduce sound by over 50% compared with insulated wood walls.
Tenants moving out due to too much noise can cost owners from $2,500 to $5,000 per unit.
That’s why more commercial construction builders are turning to ICF technologies for apartments, hotels and dorms.
More Energy Efficient
An ICF wall system can save owners up to 40% in heating and cooling costs.
Insulated concrete forms create a solid concrete wall with continuous insulation that enhances energy-efficiency and makes it ideal for multi-residential, school and commercial buildings.
ICF buildings also save 3%-5% in reduced greenhouse gas emissions over the building’s life cycle compared to wood frame construction.
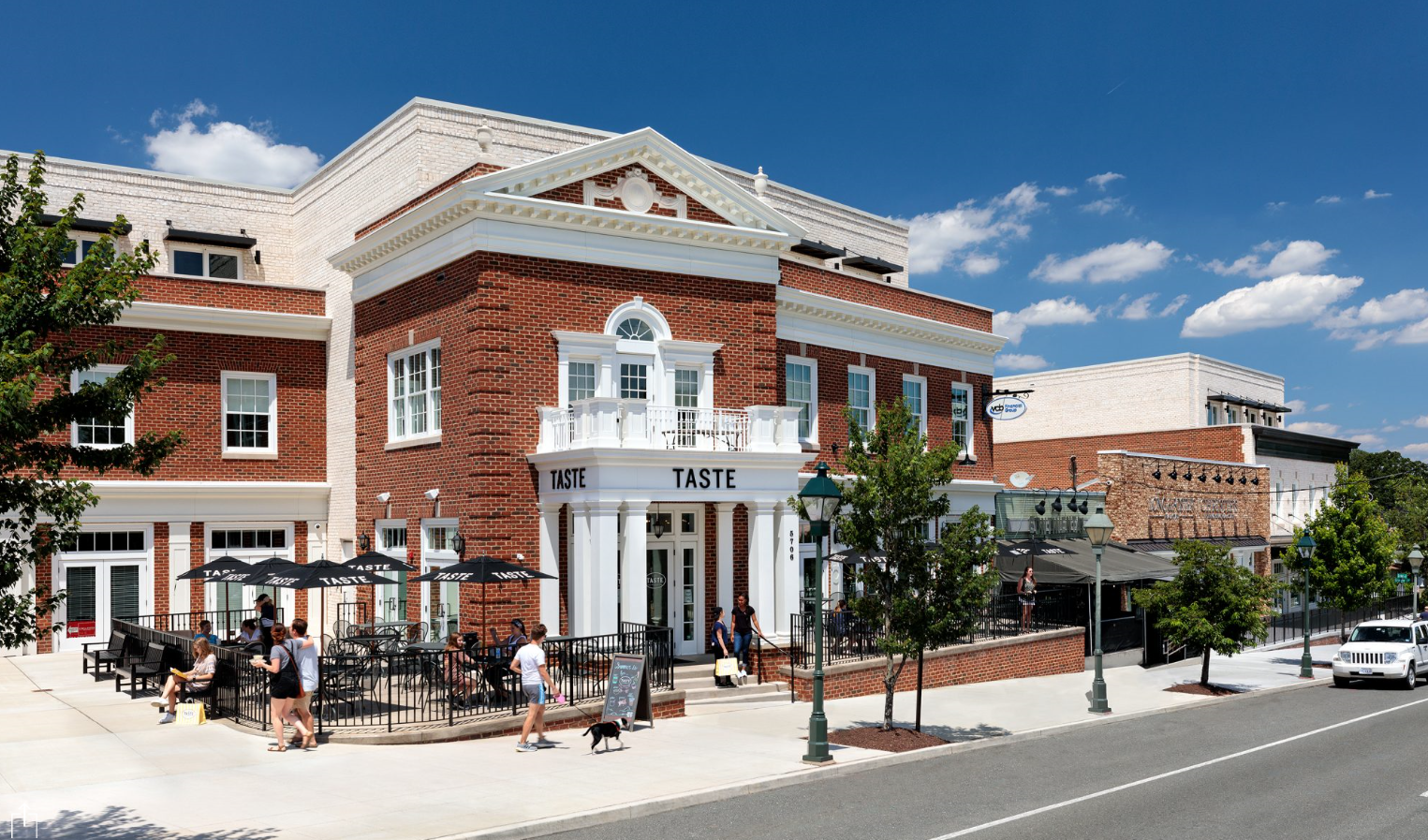
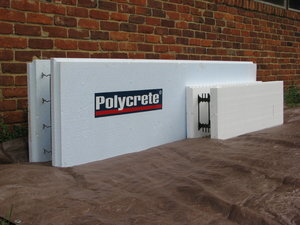
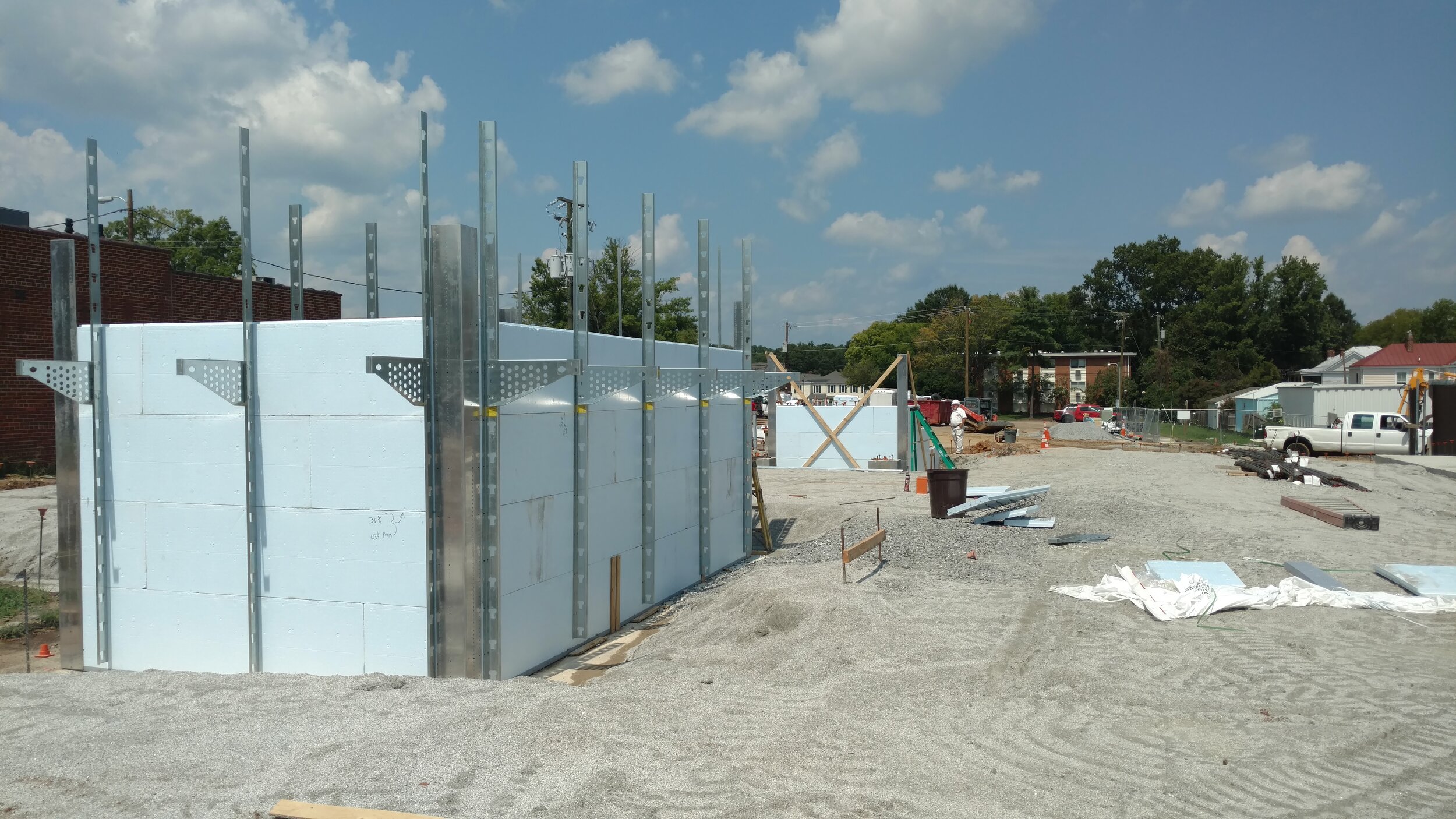
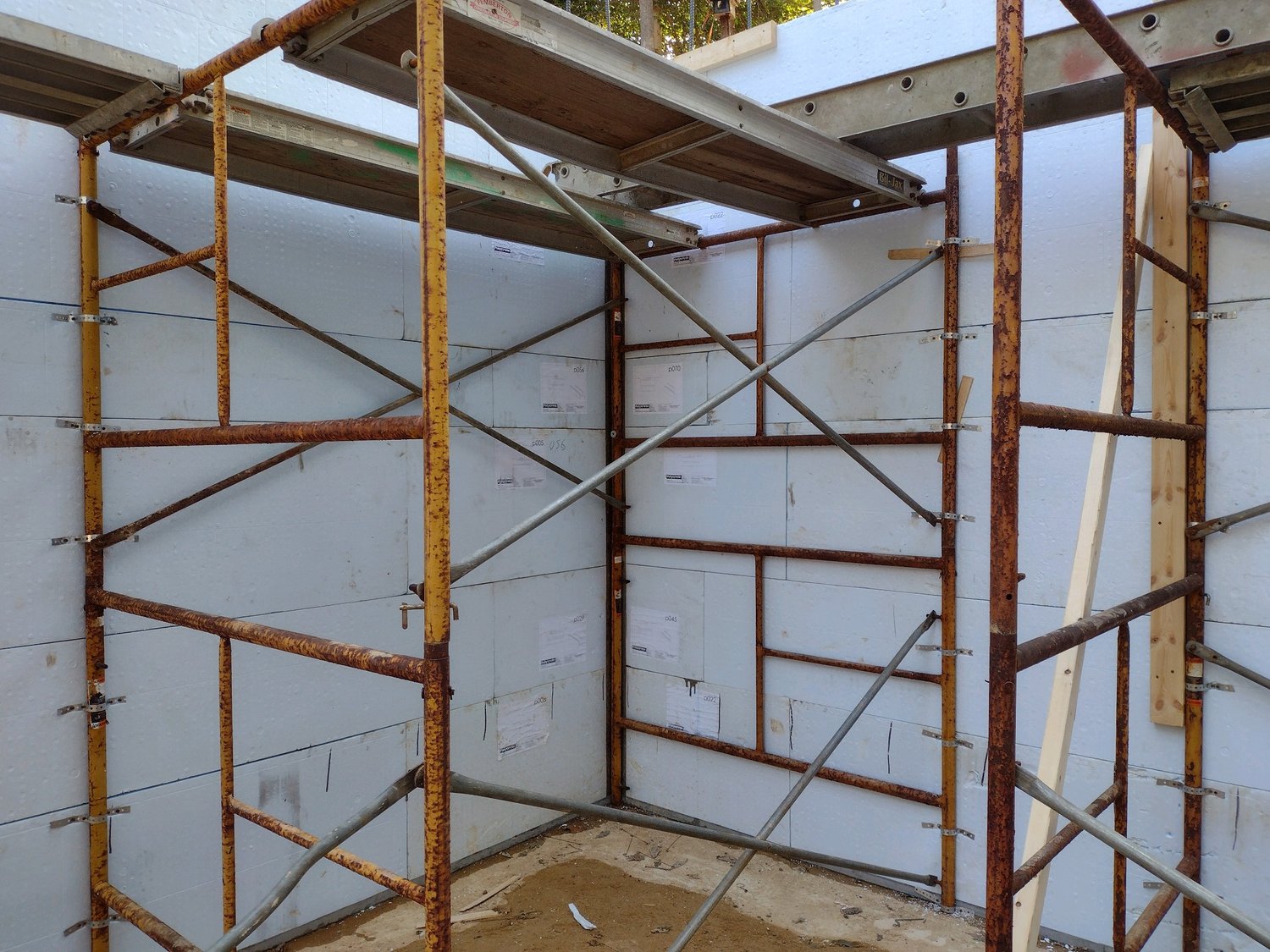
Simpler Construction
Buildings made with insulated concrete forms go up quickly and efficiently — often faster than wood framing — because ICF technologies combine six building steps into one.
Imagine completing your building’s concrete formwork, structural wall, insulation, air barrier, vapor barrier and attachment system for interior/exterior finishes all in one easy step.
ICF technologies also require less labor than wood frame construction, reducing costs and helping mitigate risk.
It’s no wonder commercial construction is turning to ICF as a better building option.
Better Materials
Steel rebar runs through the ICF/concrete wall, acting as the structural backbone.
Insulated concrete form construction can protect people and property from the devastating effects of tornadoes, hurricanes, cyclones, strong winds and earthquakes.
Unlike softwood lumber, concrete will not burn. It can take on temperatures over 1,000 degrees Fahrenheit.
Concrete also won’t rot, mold, rust or deteriorate. It’s energy efficient and virtually maintenance-free—meaning the resources you invest now will last for decades.
Less Waste
Insulated concrete forms create less waste than concrete block.
One NYC contractor says he uses just one dumpster and a part-time cleanup worker for an ICF job, compared to five dumpsters and two full-time cleanup workers for CMU construction.
He also avoids almost all waste-related violations from the Department of Buildings.
Polycrete ICFs create even less waste than others, due to their large size and horizontal fastening strips that eliminate the need to trim ends to align vertical “studs.” Factory precutting almost eliminates onsite waste altogether.
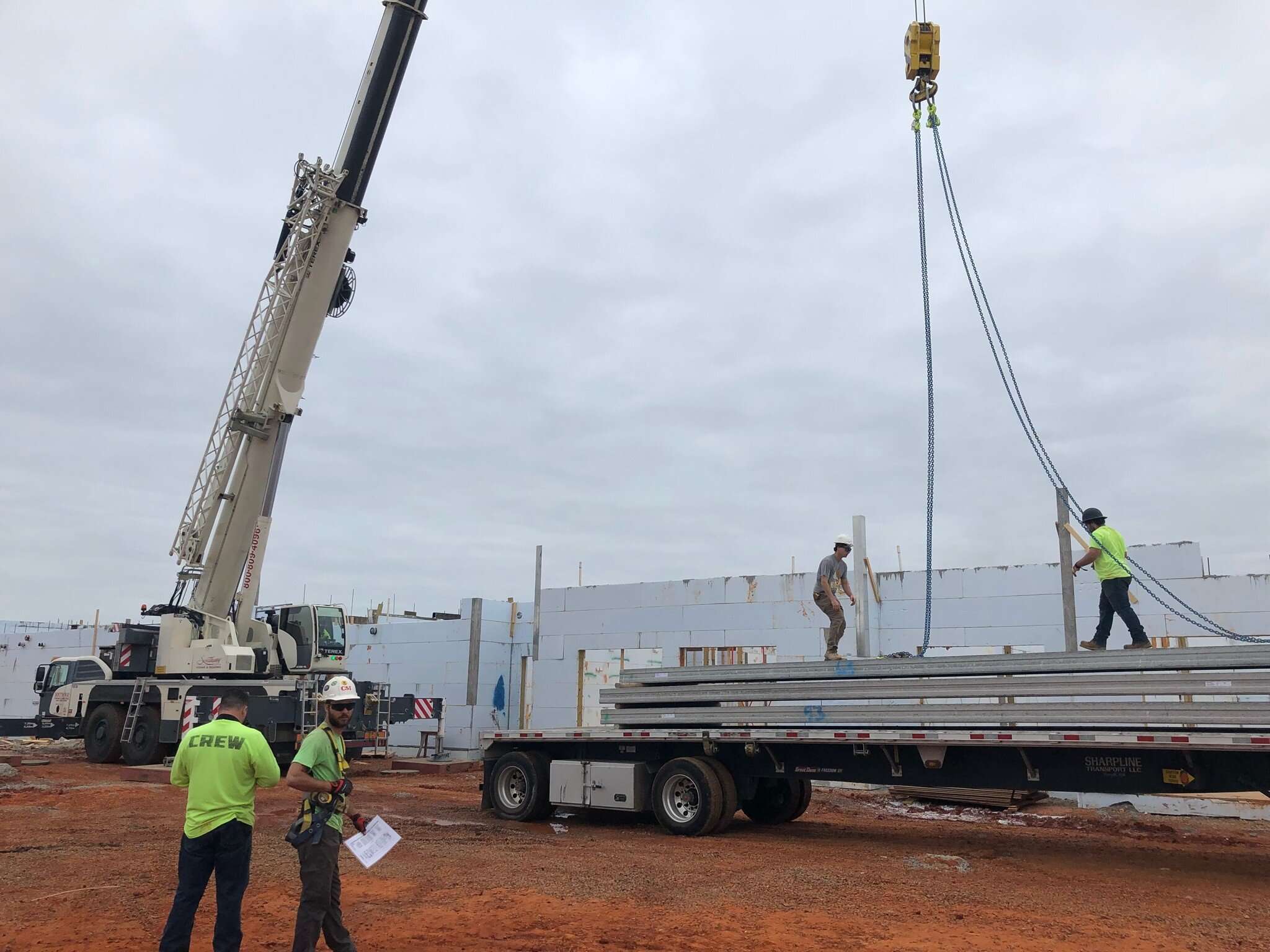
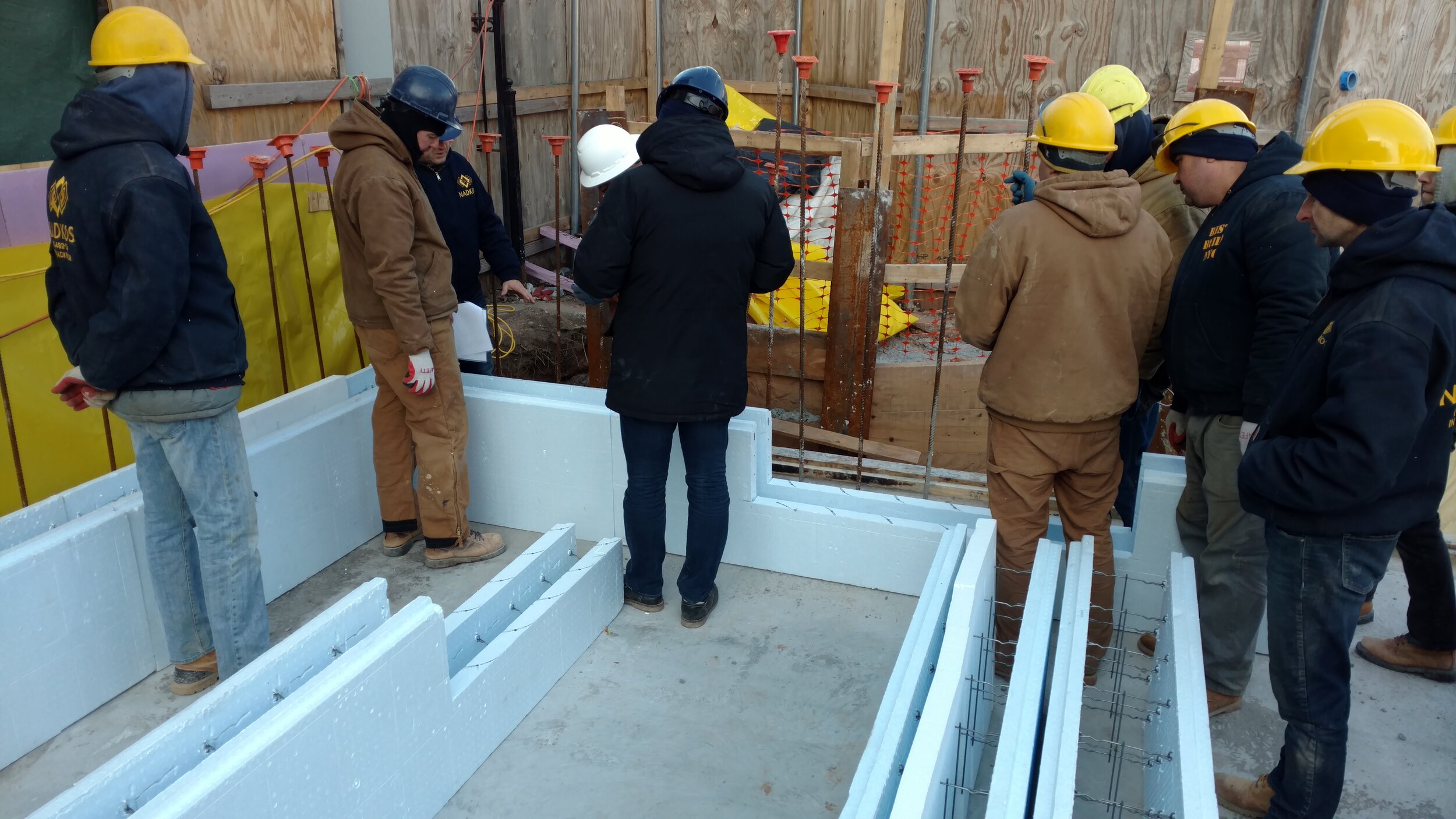
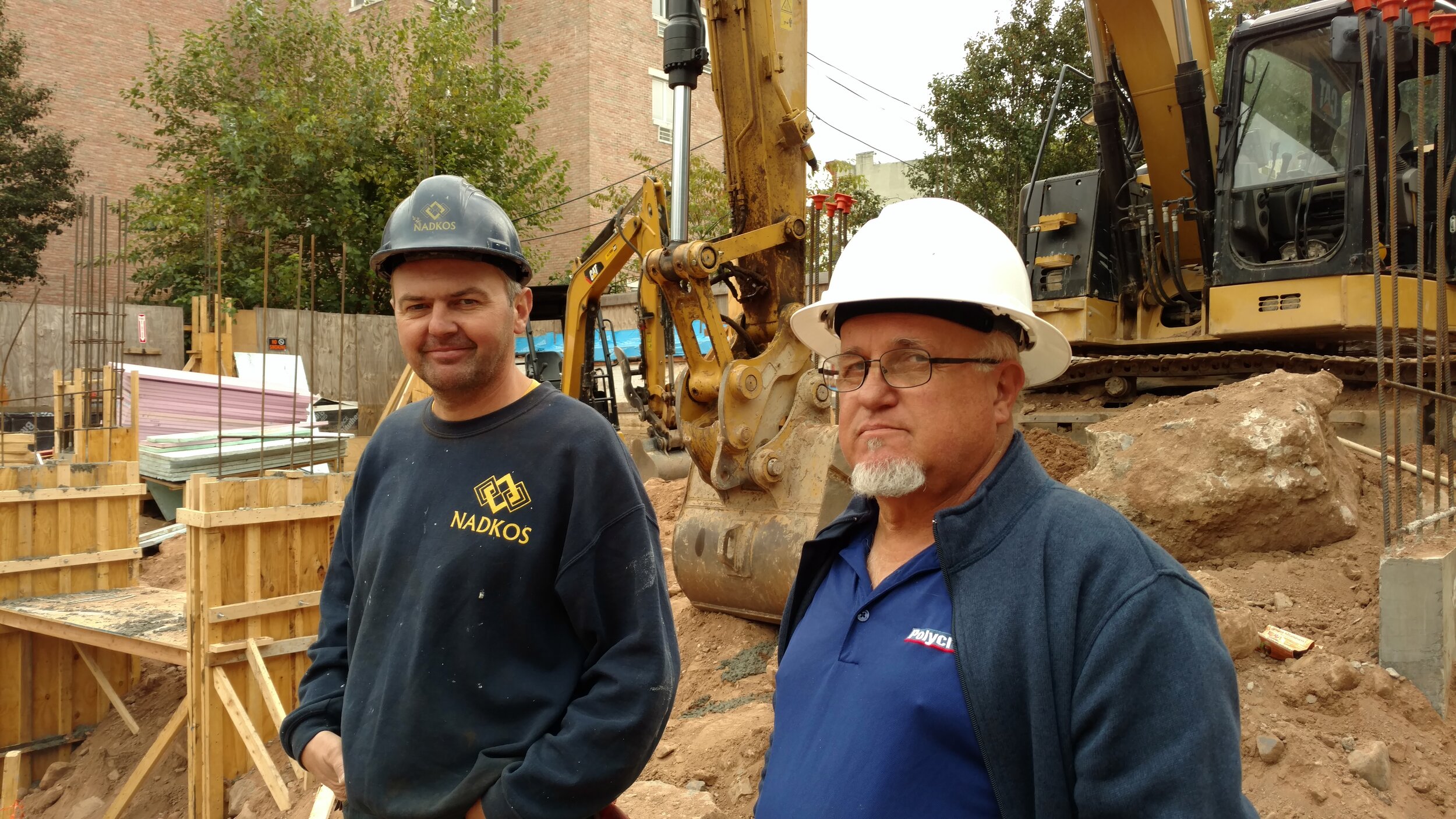
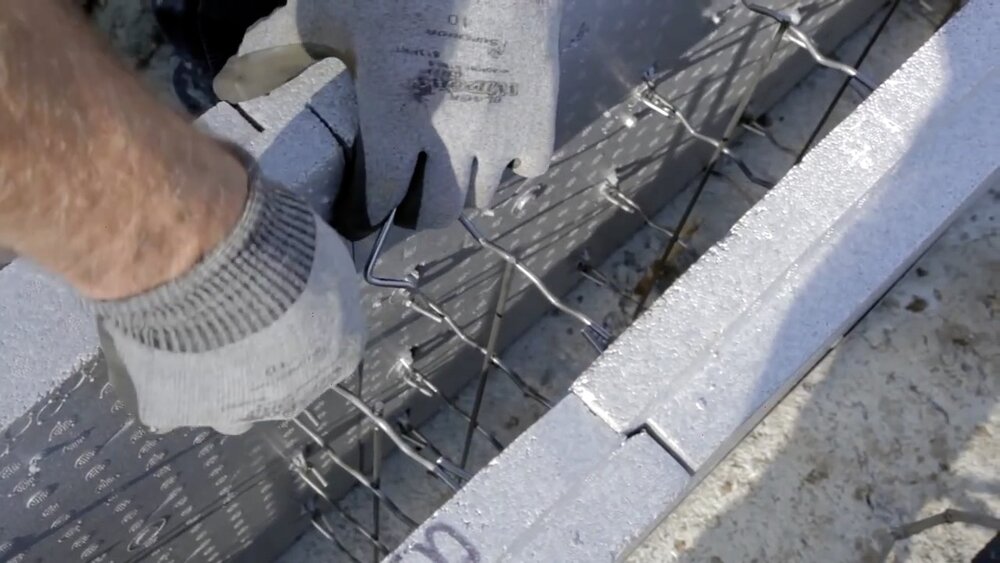
Lower Maintenance Costs
Concrete requires very little upkeep, lasts longer and has lower life cycle costs.
This is a lasting advantage for landlords and building supervisors, who benefit from energy savings as well as minimal maintenance costs by eliminating mold and moisture issues.
Upfront costs are also lower as smaller HVAC units are required due to increased energy efficiency.
Lower Insurance Costs
Concrete construction offers less risk than wood-frame construction, and that means more money saved.
Nationwide studies show that compared to wood-frame construction, mid-rise concrete buildings cost less to insure for both builders and owners.
In Edgewater, New Jersey, for instance, builders save an average of 67% on builder’s risk insurance, and owners save 58% on general liability insurance.
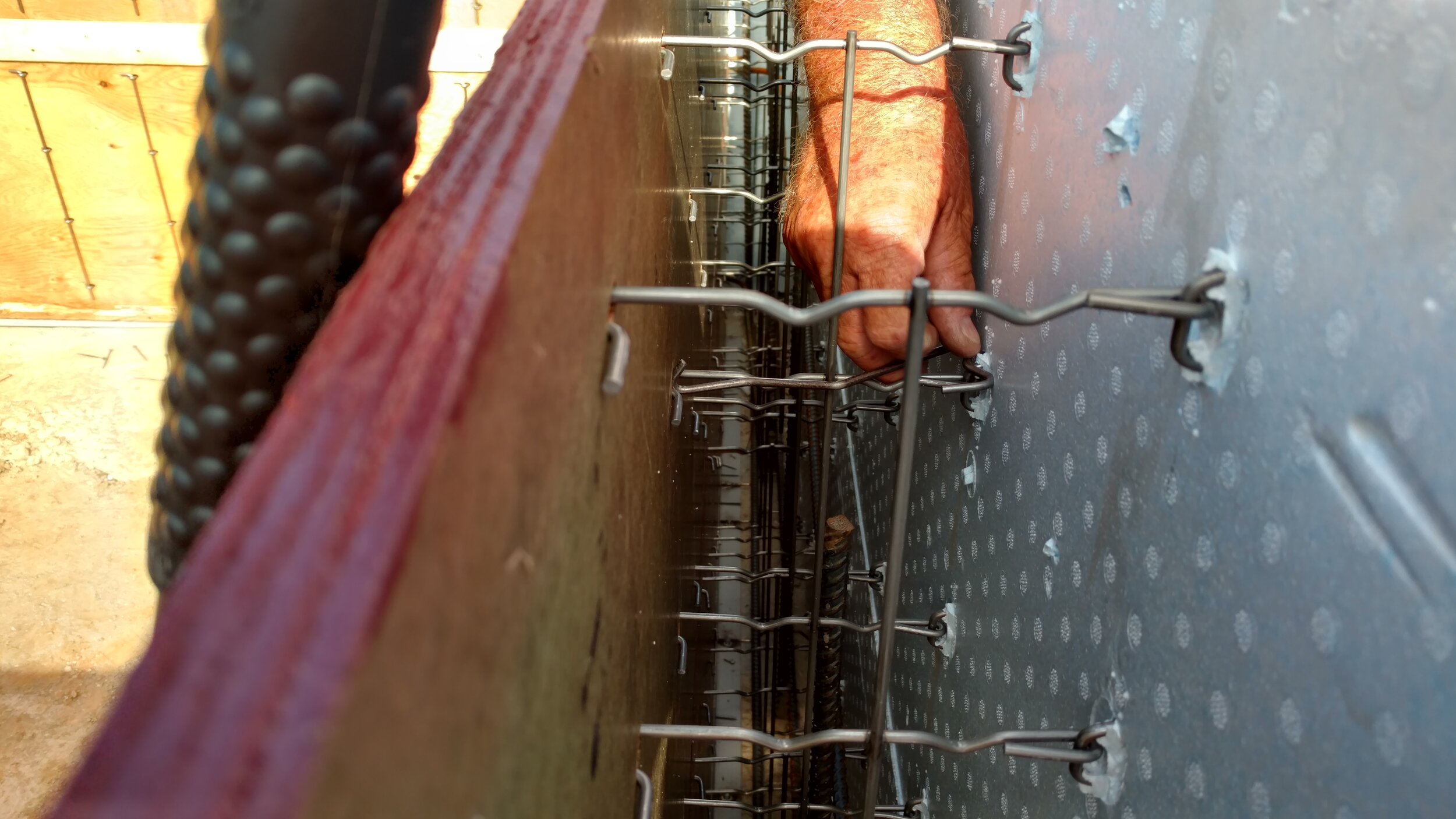
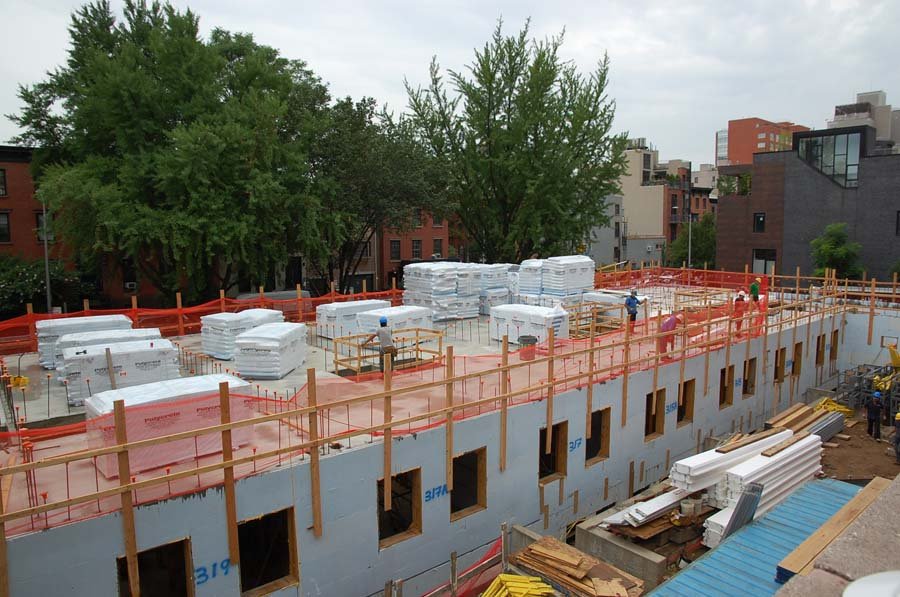
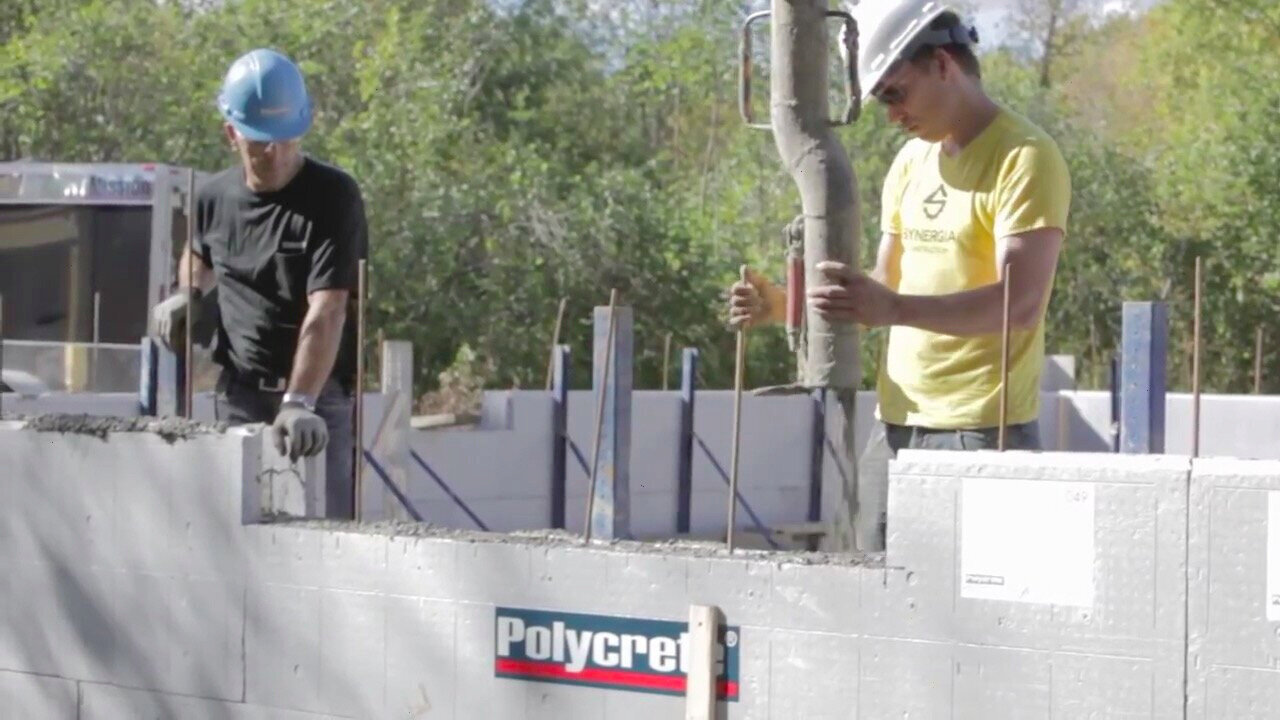
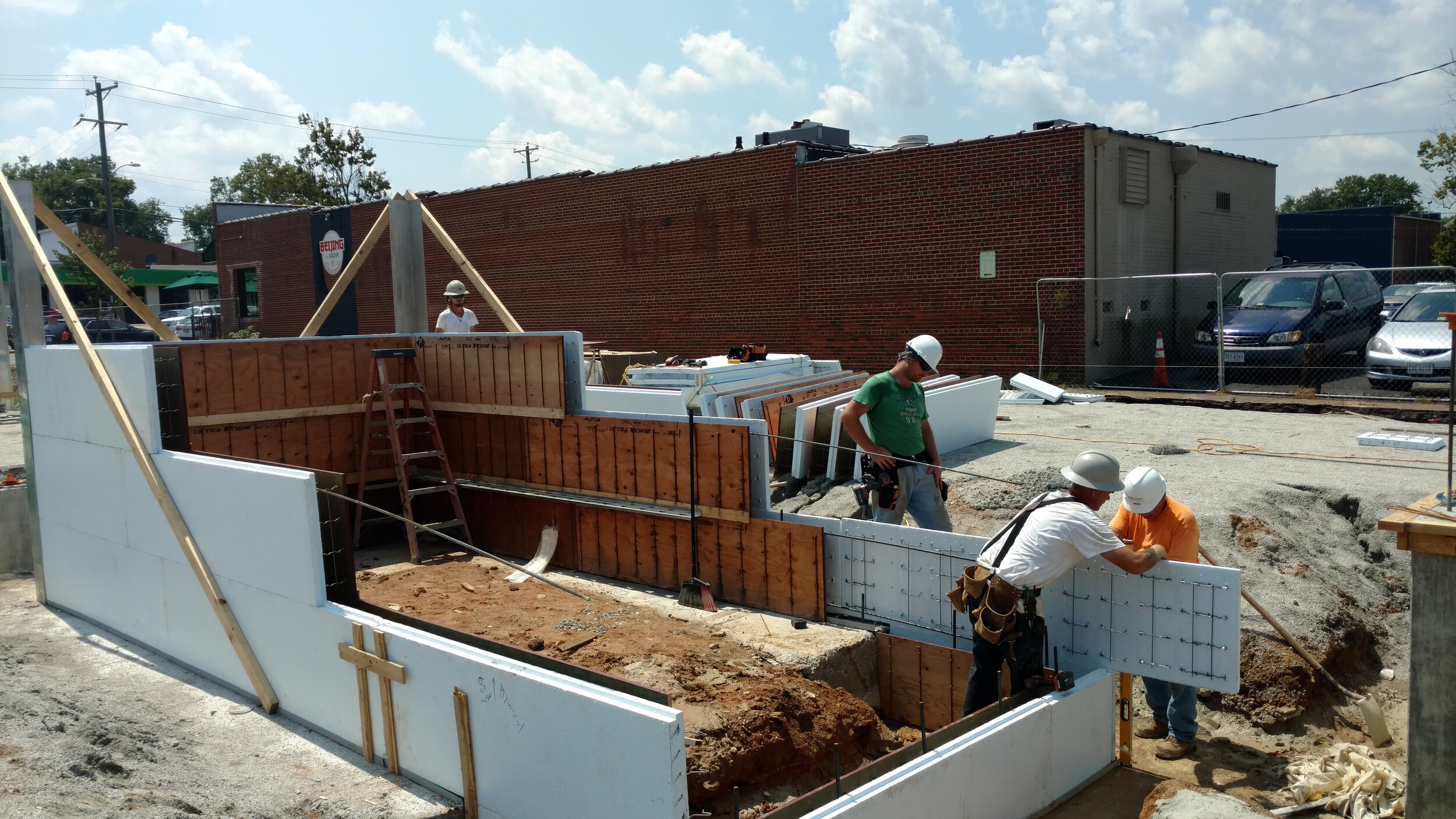
Simple Energy Code Approvals
As the largest and strongest ICFs on the market, Polycrete makes code approvals a breeze.
With a four-hour fire rating and 57 STC sound rating on a 6” wall, Polycrete meets or exceeds all local and international building codes, including the IECC 2021/COMCheck and NFPA 285.
If your local building department is unfamiliar with ICF systems, we will even help prepare the submittals package for you.
More Construction Options
Concrete thicknesses from 5-5/8” to 24.”
Insulation thicknesses of 1-3/4”, 2-1/2” and up to 18” total.
Wood, foam, or steel bucks for door/window openings.
Tall walls, radius walls and spans of over 35 feet.
We can train your crew, recommend a certified installer or build it for you.
Choose from standard ICF blocks, precut wall kits, complete structural shells or a mix.
Small Construction Footprint
Polycrete has been the choice for urban infill construction for decades.
Most work is performed from the interior of structures, enabling buildings to go up against adjacent structures in tight lot-line situations.
Polycrete ICF blocks also fold flat for shipping and storage, so greater quantities can be stored in smaller spaces and fewer trucks are sent to the jobsite.
Our experience working in urban environments means we understand how to overcome the issues and obstacles unique to city building.